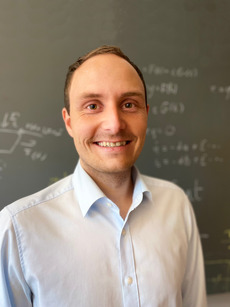
Dr.-Ing. Jens Burgert
- Postdoctoral researcher
- Office Hours:
By arrangement
- Room: 206.2
- Phone: +49 721 608-44150
- jens burgert ∂does-not-exist.kit edu
Institut für Technische Mechanik
Teilinstitut Dynamik/Mechatronik
Geb. 10.23, 2.OG
Kaiserstraße 10
76131 Karlsruhe
Curriculum vitae
03/2016 – 12/2020 | Research assistant at Institute of Engineering Mechanics of the KIT Dissertation: On direct and inverse problems related to longitudinal impact of non-uniform elastic rods Research stay over several weeks at the Angström Laboratory, Uppsala, Sweden and at the Technical University Tampere, Finland |
01/2016 – 02/2016 | Englisch teacher AIES International, Vietnam |
04/2013 – 10/2015 | Mechanical Engineering study at Karlsruhe Institute of Technology Majoring in: Theoretical Mechanical Engineering Main focus: Dynamic and vibrations and cognitive technical systems Degree: Master of Science with distinction Master thesis: Model-based development of a systematic approach to optimize electrical drive systems with variable operation voltage |
09/2013 – 05/2014 | Study abroad at Heriot-Watt University Edinburgh, Scotland |
04/2013 – 08/2013 | Student employee at Robert-Bosch GmbH, Bühlertal Setup of a parametric tailgate model using ADAMS |
10/2009 – 03/2013 | Mechanical Engineering study at Karlsruhe Institute of Technology Main focus: Dimensioning and validation of mechanical constructions Degree: Bachelor of Science Bachelor thesis: Implementation of the thermo-mechanical load on a clutch pressure plate: main focus thermal calculation |
10/2012 – 03/2013 | PreMaster at Robert-Bosch GmbH, Bühl Noise examination and modeling of an electrical low power motor |
Research interests
Impacting rods are used in various devices in practical life. One example is rock drilling, where a piston is accelerated hydraulically or pneumatically before it hits the drill rod. The hit is followed by a complicated sequence of phenomena. A stress wave, whose length is double the physical length of the piston, starts to propagate along the drill rod to finally reach the tool-process material interface. A nonlinear penetration of the bit into the rock takes place and a reflecting wave component is generated.
In the long history of rock drilling, fundamental mechanisms contributing to the effective drilling process are still unknown. To produce maximal tool penetration for each hit, rules have to be derived which specify the dimensioning of the piston and drill rod. Recent investigations, that cover the issue of optimization, are revealing that the efficiency of the drilling process strongly depends on the shape of the longitudinal wave transmitted through the drill rod to the drill bit. A well-known fact is that the cross-sectional profile of the piston is shaping the stress wave profile. Therefore, the main object of the research project is to adjust the geometrical form of the impacting piston to generate every desired stress wave form. This is an inverse problem as the cause (geometry of the piston) is concluded from the consequence (stress wave form after impact). For inverse problems, it needs to be examined if a solution exists and if the solution is unique.
A test rig is set up in order to validate the theoretical results. The stress wave from is derived from the strain gauges (SG) signal which is further processed with a signal conditioner. By recording the hit with a high-speed camera, the time when piston and rod separate may be detected. Besides, the high-speed camera is able to validate the theoretical calculations which predict that the rod moves discontinuously after the hit.
Monograph
Burgert, J.
2021. KIT Scientific Publishing. doi:10.5445/KSP/1000129237
Publications
Burgert, J.; Seemann, W.
2019. Proceedings in applied mathematics and mechanics, 19 (1), Articel: e201900007. doi:10.1002/pamm.201900007
Burgert, J.; Seemann, W.
2019. 26th International Congress on Sound and Vibration 2019 (ICSV26), Montreal, Canada, 7 - 11 July 2019, 199–206, Curran
Burgert, J.; Seemann, W.
2018. Proceedings in applied mathematics and mechanics, 18 (1), e201800250. doi:10.1002/pamm.201800250
Burgert, J.; Seemann, W.; Moilanen, C.; Montonen, J.; Miettinen, J.; Saarenrinne, P.
2018. Proceedings of ISMA2018, International Conference on Noise and Vibration Engineering/USD2018, International Conference on Uncertainty in Structural Dynamics : Leuven, Belgium, 17 - 19 September, 2018. Ed.: W. Desmet, 3535–3547, KU Leuven
Burgert, J.; Seemann, W.; Hartenbach, F.
2017. Proceedings in applied mathematics and mechanics, 17 (1, SI), 675–676. doi:10.1002/pamm.201710306
Graduant | Title | Type | Date |
---|---|---|---|
Dragos-Corneliu Ana |
Implementation of a numerical method to model bending waves in beams based on the Wave Finite Element Method | Bachelor thesis | 2020 |
Eric Pihuave |
Experimental investigation of wave propagation phenomena in different materials | Bachelor thesis | 2019 |
Aykut Demirkol |
Experimental investigation of the influence of the piston geometry on the wave propagation of impacting rods | Bachelor thesis | 2019 |
Frederic Cüppers |
Comparison of different modelling approaches for longitudinal impact of non uniform rods | Bachelor thesis | 2020 |
Betreute Lehrveranstaltungen
WS 21/22 | Mechatronik-Praktikum |
SS 2021 | Übungen zu Mathematische Methoden der Schwingungslehre |
SS 2020 | Übungen zu Mathematische Methoden der Schwingungslehre |
WS 19/20 | Übungen zu Technische Schwingungslehre |
SS 19 | Übungen zu Mathematische Methoden der Schwingungslehre |
WS 18/19 | Mechatronik-Praktikum |
SS 18 | Übungen zu Experimentelle Dynamik |
SS 18 | Schwingungstechnisches Praktikum |
WS 17/18 | Übungen zu Einführung in die Technische Mechanik II: Dynamik |
SS 17 | Engineering Mechanics IV (Tutorial) |
SS 17 | Übungen zu Technische Mechanik IV |
WS 16/17 | Engineering Mechanics III (Tutorial) |
WS 16/17 | Übungen zu Technische Mechanik III |
SS 2016 | Workshop 'Arbeitstechniken im Maschinenbau' (ITM, Fidlin) |
SS 2016 | Workshop 'Arbeitstechniken im Maschinenbau' (ITM, Seemann) |